ОКАЛИНА. КАК УЛУЧШИТЬ КАЧЕСТВО РЕЗКИ?
ИСПОЛЬЗУЙТЕ ОБОРУДОВАНИЕ HYPERTHERM С МАКСИМАЛЬНОЙ ЭФФЕКТИВНОСТЬЮ
Некоторые проблемы с качеством резки вызваны проблемами с механикой и электрической частью старых или плохо обслуживаемых машин для резки, другие проблемы связаны с самим процессом резки. Если в уравнении для качества резки так много неизвестных, возникает вопрос: каким образом начать поиск и устранение проблем? В данной статье мы рассмотрим критически важные переменные процесса, которые влияют на качество резки. Тщательно контролируя эти переменные, Вы можете минимизировать или устранить проблемы и, соответственно, связанные с ними затраты на доработку деталей или их утилизацию.
В процессе удаления окалины многие ремонтные мастерские тратят уйму времени и денег на шлифование, зачистку дефектов и пескоструйную очистку деталей, которые вырезаны на машине плазменной резки. Если в уравнении для качества резки так много неизвестных, возникает вопрос: каким образом оператору резака плазменной резки начать поиск и устранение проблем с образованием окалины? Тщательно контролируя критически важные переменные процесса, оператор может минимизировать или устранить образование окалины и, соответственно, связанные с этим затраты на доработку деталей.
Окалина — это отвердевший окисленный расплавленный металл, который остается в разрезе при выполнении резки. Эта самая распространенная проблема качества плазменной резки. Окалина может образовываться в виде больших пузырчатых отложений вдоль нижней кромки листа (так называемая «окалина низкой скорости резки»), небольших затвердевших полосок вдоль неразрезанного материала («окалина высокой скорости резки») или тонкого покрытия вдоль верхней поверхности листа («верхнее забрызгивание»).
Образование окалины зависит от многих переменных процесса, включая скорость перемещения резака, расстояние между резаком и заготовкой, силу тока, напряжение и состояние расходных деталей. На него также влияют характеристики материала, например, его толщина и тип, марка, химический состав, состояние поверхности, плоскостность и даже изменения температуры материала при его резке. Но наиболее существенно на образование окалины влияют три характеристики: скорость резки, сила тока и расстояние между резаком и заготовкой.
Окалина низкой скорости
Если скорость резки слишком низкая, плазменная струя начинает «искать» дополнительный материал для резки. Столб плазменной дуги увеличивается в диаметре, расширяя разрез до такой ширины, при которой высокоскоростной сегмент плазменной дуги больше не может выдувать расплавленный материал из разреза. В результате расплавленный материал начинает скапливаться вдоль нижней кромки листа в форме шарообразных скоплений толстого слоя. Такая окалина называется окалиной низкой скорости. На слишком низких скоростях резки дуга гаснет, поскольку недостаточно металла для поддержки дуги прямого действия. Повышение силы тока или уменьшение расстояния между резаком и заготовкой (при одинаковой толщине материала и скорости резки) имеет точно такое же влияние, как и уменьшение скорости резки. Каждое из этих изменений приводит к тому, что в данный момент времени больше энергии воздействует на данную область. Слишком высокая сила тока или слишком маленькое расстояние от резака до заготовки также могут привести к образованию окалины низкой скорости. (Образование небольшого количества окалины в углах траектории плазменной резки — нормальное явление, поскольку при резких поворотах резака невозможно сохранить скорость постоянной).
Чтобы исключить образование окалины низкой скорости:
- Увеличьте скорость резки пошагово с шагом 125 мм/мин
- Увеличьте расстояние между резаком и заготовкой пошагово с шагом 1,6 мм или 5 В
- Уменьшите силу тока пошагово с шагом 10 А
- Если качество резки не удается улучшить ни одним из указанных действий, рассмотрите вариант использования сопла меньшего размера
Окалина высокой скорости
Если скорость резки слишком большая, дуга начнет запаздывать с перемещением по разрезу, что приведет к образованию небольших затвердевших полосок несрезанного материала или перекатывающейся окалины вдоль нижней кромки листа. Окалина высокой скорости более устойчива к воздействию. Для ее снятия, как правило, необходима серьезная механическая обработка. При слишком высоких скоростях резки дуга становится нестабильной: в разрезе длина ее столба то увеличивается, то уменьшается, что приводит к образованию «продольного гребня» искр и расплавленного материала. Дуга может не прожечь металл на всю толщину или погаснуть.
Большое расстояние между резаком и заготовкой или низкая сила тока (для данной толщины материала и скорости резки) также может привести к образованию окалины высокой скорости, поскольку оба эти изменения приводят к уменьшению энергии плазменной струи.
Чтобы исключить образование окалины высокой скорости:
- Проверьте сопло на наличие признаков износа (выемки, превышение номинального размера или овальное отверстие)
- Уменьшите скорость резки пошагово с шагом 125 мм/мин
- Уменьшите расстояние между резаком и заготовкой пошагово с шагом 1,6 мм или 5 В
- Повысьте силу тока (при этом она не должна превышать 95 % от номинального значения для сопла с данным отверстием)
Окалина, образующаяся вследствие верхнего забрызгивания
Верхнее забрызгивание — это скопление отвердевшего металла, который разбрызгивается вдоль верхней поверхности заготовки. Снятие этого вида окалины не представляет сложностей. Причины образования этой окалины: слишком высокая скорость резки или большое расстояние между резаком и заготовкой. Она образуется вследствие воздействия вихревого потока плазменной струи, которая при определенном угле атаки выталкивает расплавленный материал из передней части разреза, а не проталкивает его вглубь разреза.
Чтобы исключить образование верхнего забрызгивания:
- Проверьте сопло на признаки износа
- Уменьшите скорость резки пошагово с шагом 125 мм/мин
- Уменьшите расстояние между резаком и заготовкой пошагово с шагом 1,6 мм или 5 В
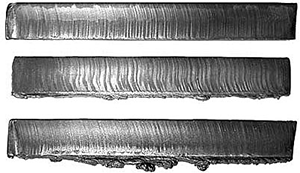
На рисунке представлено влияние скорости резки на качество резки. Рассмотрим подробнее:
- Верхний слой- использовалась правильная скорость резки.
- Средний слой - слишком высокая скорость резки
- Нижний слой- слишком низкая скорость резки
Окно без образования окалины
Между высокой и низкой скоростью резки, при которых образуется окалина, есть определенный диапазон (окно) скоростей резки, при которых окалина не образуется или образуется в минимальном количестве. Установить это окно — основная задача в стремлении минимизировать доработку деталей, вырезанных с использованием систем плазменной резки.
Данное окно зависит от плазмообразующего газа, например, азот и воздух как плазмообразующие газы имеют сравнительно узкое окно отсутствия образования окалины при резке низкоуглеродистой стали, в то время как для кислорода (в качестве плазмообразующего газа) это окно шире. Кислород, как плазмообразующий газ, вступает в реакцию с низкоуглеродистой сталью, в результате чего образуются небольшие брызги: каждая капля имеет меньшее поверхностное натяжение. Эти расплавленные брызги легче выдуваются из разреза.
На окно без образования окалины также влияет тип материала. Например, при резке холоднокатаной или травленной стали образуется меньше окалины, чем при резке горячекатаной или нетравленной стали.
Как определить оптимальную скорости резки?
- Метод №1. Выполните несколько последовательных операций резки на различных скоростях резки и выберите скорость, при которой образуется меньше всего окалины. Линии задержки (небольшие гребни на поверхности резки) — хороший индикатор скорости резки. При низких скоростях резки образуются вертикальные линии задержки, которые перпендикулярны плоскости листа. На высоких скоростях резки образуются наклонные S-образные линии задержки, которые расположены параллельно листу вдоль нижней кромки. Изучив линии задержки, оператор может определить, как изменить скорость (увеличить или уменьшить), чтобы найти окно без образования окалины. Многие операторы имеют привычку замедлять машину, как только начинает появляться окалина, однако часто требуется повысить скорость.
- Метод №2. Наблюдайте за дугой (через защитный сварочный щиток) во время резки и существенно измените скорость, чтобы получить оптимальные характеристики дуги. Для этого обратите внимание на угол, под которым дуга выходит из заготовки. Если в качестве плазмообразующего газа используется воздух, то при выходе с нижней стороны листа дуга должна быть вертикальной. Если в качестве плазмообразующего газа используется азот или смесь аргон/водород, то наилучшим вариантом является небольшое отставание дуги. Для кислорода в качестве плазмообразующего газа наилучшей скоростью резки будет та, при которой дуга слегка уходит вперед.
Надеемся, что данная статья была для вас полезной и вы избежите процесса образования окалины.